11. April 2020
Da ich letztes Jahr in den Besitz einer wunderschönen Avonds F-15 mit Turbine
gekommen bin, stand die Frage im Raum, weshalb nicht erst mit einem Trainer
das Turbinenfliegen üben, um die F-15 zu schonen? Da Kollege Mailman mit der
P60 Jetmietze in seiner TopRC Cougar leistungsmässig nicht zufrieden war, hat er
diese durch eine stärkere Kingtech Turbine ersetzt. Die Jetcat brauchte einen
neuen Flieger. Was passte besser, als diese mir anzubieten (Besten Dank an
dieser Stelle!), damit sie den entsprechenden Flieger befeuern kann?
Nur – dieser musste noch gefunden werden. Der Markt für diese Schubklasse ist
äusserst dünn. Die Jet Power Messe war auch nicht besonders ergiebig. Kurz vor
der Aufgabe bin ich dann doch noch bei PAF auf die Sting Evo gestossen, der
perfekt zu einer 6kg Turbine passte. Hätte PAF dieses Modell an der Messe
dabeigehabt, ich hätte schon früher zuschlagen können!
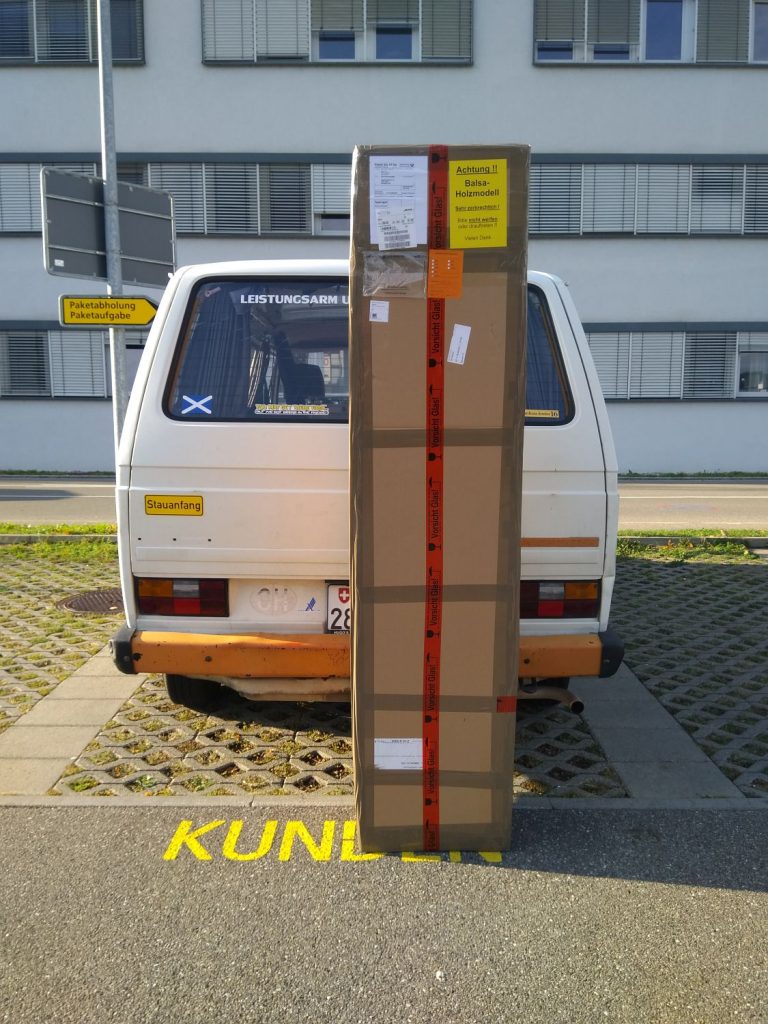
Mitte Oktober 2019 durfte ich dann bei der DHL mit einem strahlenden Gesicht
(nein, nicht nur weil ich kurz vorher Tschernobyl besucht habe…) mein Paket
entgegennehmen. Fahren sie doch rüber zur Rampe, haben sie gesagt, das
Paket ist riiiiesig. Ich bin dann rübergelaufen und hab das Paket ein paar
hundert Meter über den Platz getragen….ich wusste ja, dass das Packmaterial
das schwerste daran ist 😉
Kurz darauf habe ich zufällig auf unserem Modellflugplatz erfahren, dass einer
von uns auch schon eine Sting erbaut und geflogen hat. Es war eine
Erleichterung, aus erster Hand zu erfahren, dass das Ding auch gut fliegt und auf
Bautips zurückgreifen zu können.
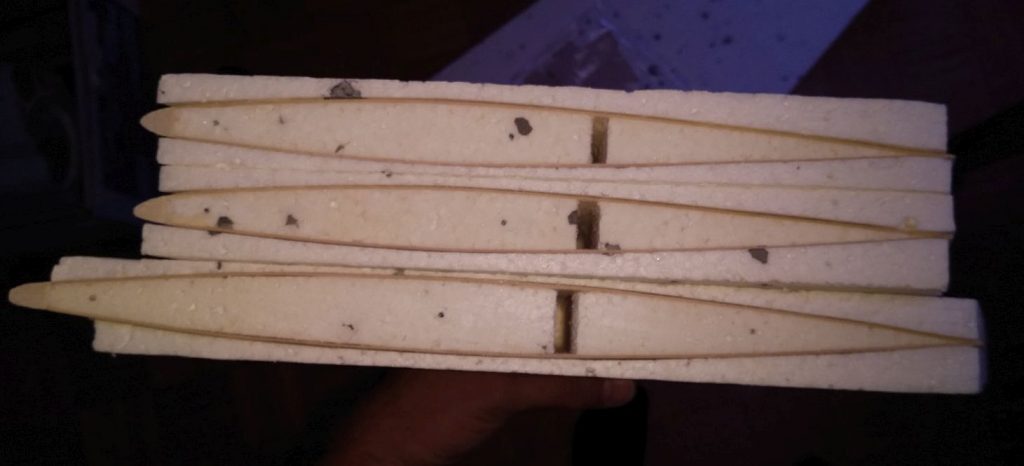
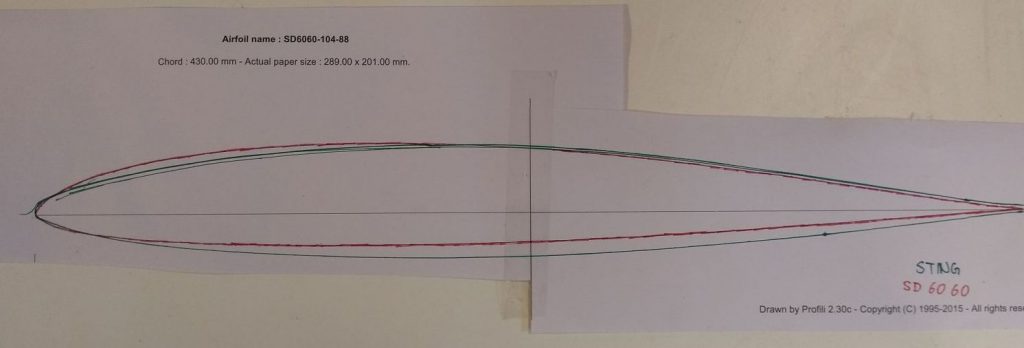
Als erstes fielen mir die komischen Profile auf. Oben die Leitwerke, unten das
Flügelprofil an der Wurzel im Vergleich zu einem SD6060, dass es eigentlich, laut
Modellbeschrieb sein müsste. Da war wohl ein Laminarprofilfanatiker am Werk.
Bisschen optimistisch für unsere Reynoldszahlen, aber naja.
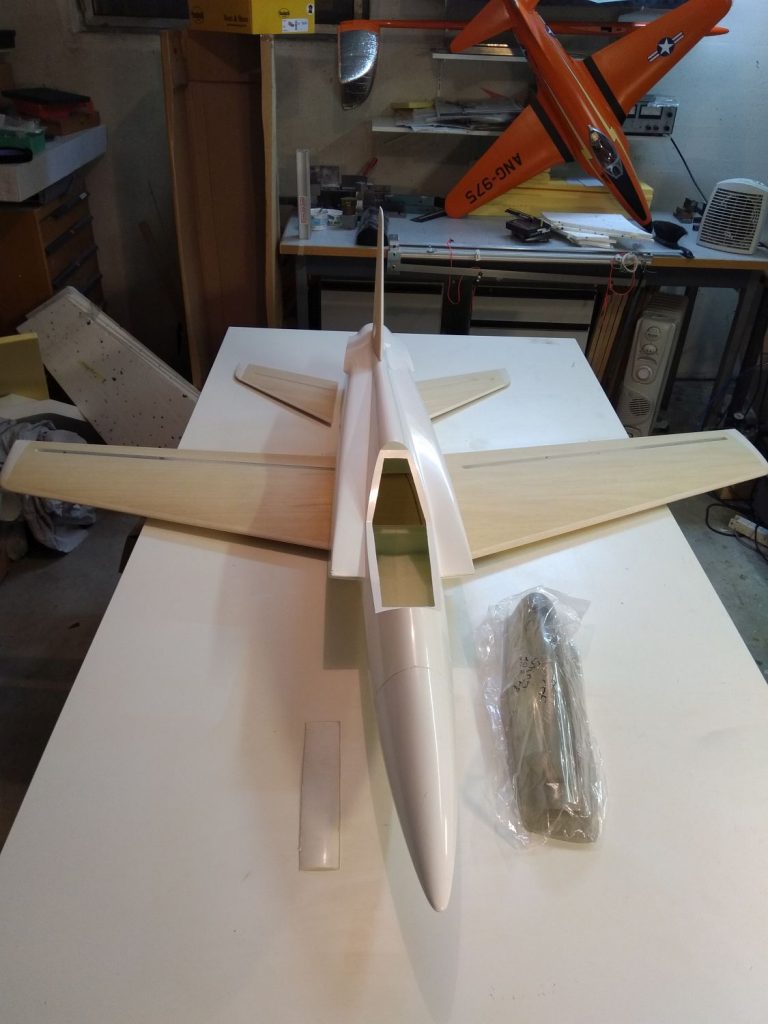
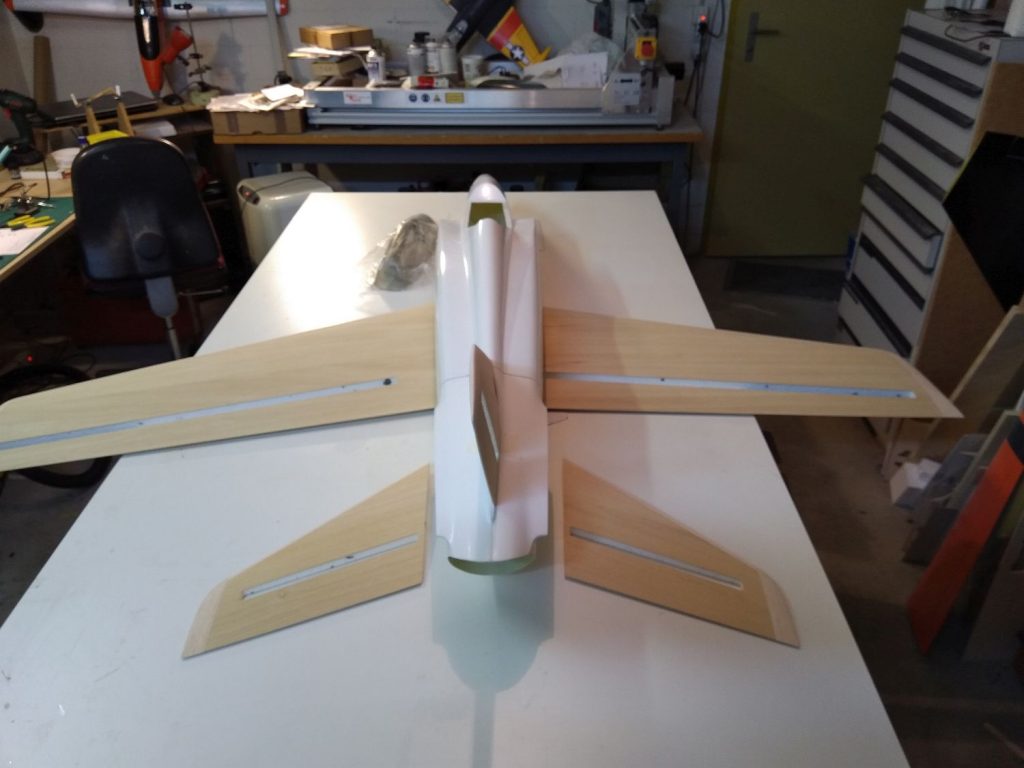
Hier der Bausatzinhalt ohne Spantensatz (den hab ich mitbestellt und der ist
tadellos verarbeitet + passend). Man beachte die fetten Ausfräsungen für die
Verkastungen. Das muss praktisch vollständig mit schwerem Balsa gefüllt
werden. Ein bisschen weniger hätte nicht geschadet. Die Flügel sind perfekt
verarbeitet, die Randbögen und Nasenleisten bereits genau verschliffen.
Zwischen der Beplankung und dem Styrokern befindet sich Glasgewebe! Der
Rumpf ist gefühlt sehr leicht, aber doch fest genug. Leider sind die Nähte etwas
prominent. Die Anleitung ist eher dürftig, aber ausreichend, wenn man schon
das eine oder andere Modell gebaut hat.
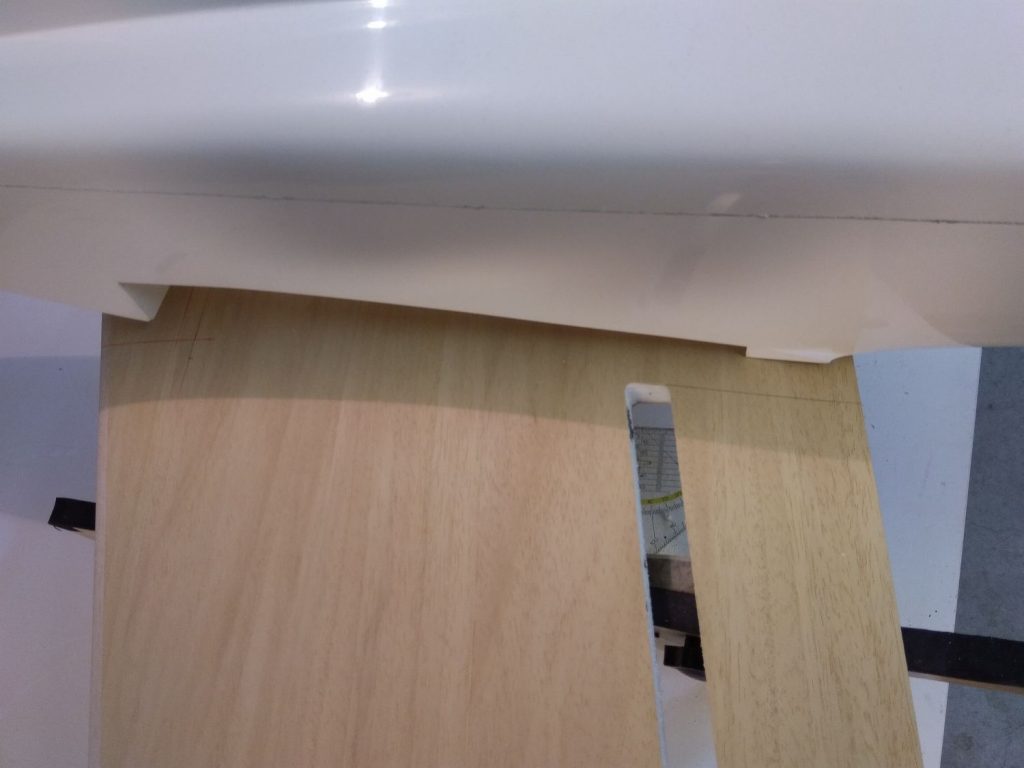
Beim Flügel muss noch einiges ausgeschnitten werden, dass er auch unter den
Rumpf passt. Leider passen die Masse der Anleitung nicht zum Rumpf, es fehlen
ca. 8mm. Diese könnte man vorne oder hinten ausschneiden, leider verschiebt
sich somit auch der Schwerpunkt. Das wollte ich schon genau wissen. Nach
Rücksprache mit Peter Adolfs ist die Referenz die kleine Endleistenanformung
am Rumpf, die zur Endleiste passen muss. Somit war der Fall klar, wie die
Ausschnitte zu legen sind. Aufpassen muss man lediglich, dass man nicht die
Rumpfnaht als Referenz nimmt, denn die ist nicht genau mittig.
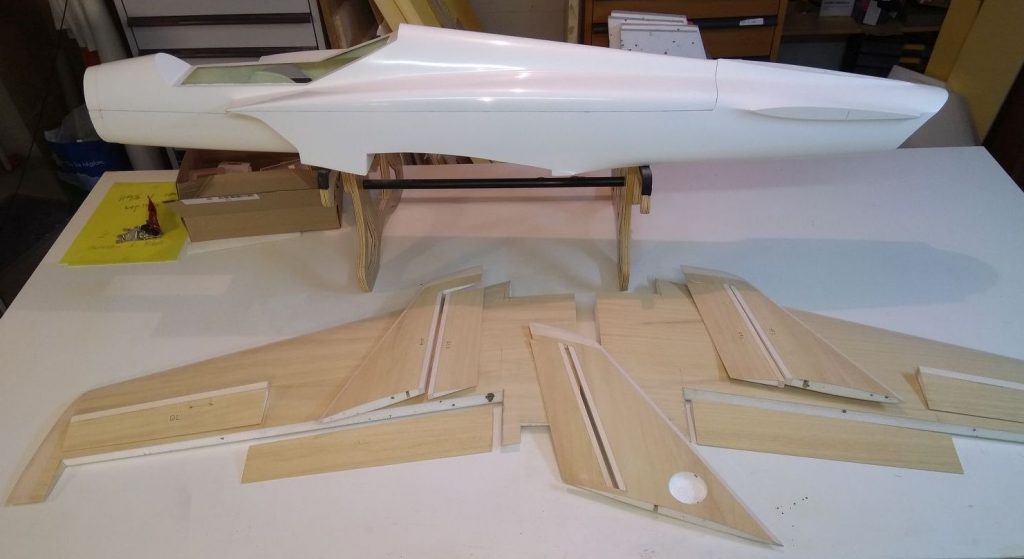
Die Spalten sind am Leitwerk 16mm, am Flügel 20mm breit. So kann man die
Verkastungsleisten aus 8mm bzw. 10mm Balsabrettchen ausschneiden. Was man
nicht sieht, sind die Ruderseitigen Verstärkungen an den Orten, wo die
Ruderhörner voraussichtlich hinkommen werden. Dazu habe ich etwas Styro
herausgefräst und einen Balsakeil eingeharzt.
Vor dem Verkasten muss man sich noch Gedanken machen, wie man die Ruder
überhaupt lagert und anlenkt: Keilförmig mit Spalt, Hohlkehle, V-Anschliff, sogar
Spaltklappen? Der Einfachheit halber habe ich mich für klassisch mit Spalt
entschieden, mit Silikonscharnier (ausser beim Seitenruder). Das Modell soll ja
auch mal fertig werden…
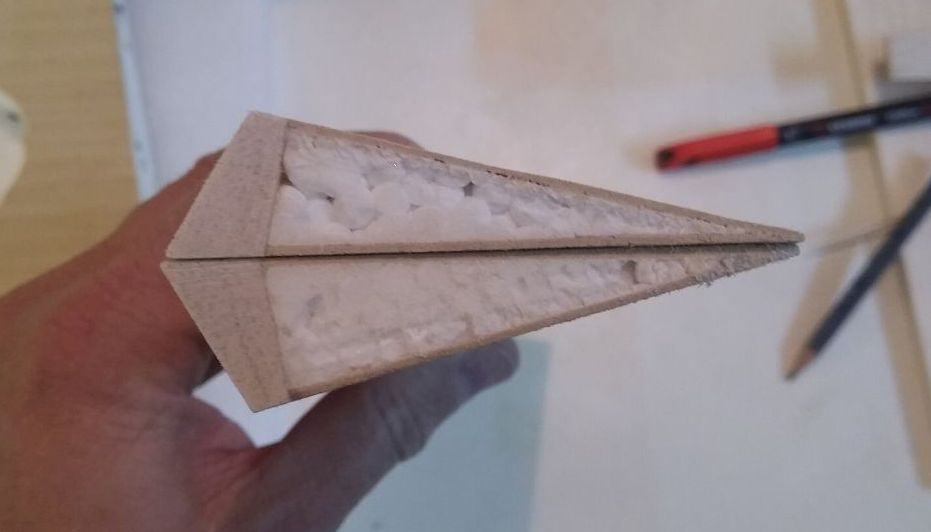
Ich bin erstaunt, wie genau ich schleifen kann 😀

Schon früh wollte ich wissen, wie das Fahrwerk eingebaut werden muss, wo, und
ob da schon Verstärkung drin sind. Die Anleitung schweigt darüber. Immerhin ist
beim Ausschnitt schon ein Teil des Styros draussen, somit konnte ich mit meiner
Turbotaschenampe mit 2,6 Kilolumen den Flügel röntgen, die Konturen
nachzeichnen und ausfräsen.
Apropos Fräsen, ich mach das alles mit einem Dremel und einem
Diamantbeschichteten und Diamantverzahnten 2mm VHM-Fräser. Der geht wie
Butter durch Holz und GFK/CFK, lässt sich leicht freihändig führen und hat wenig
Neigung, auszureissen. Damit schneide ich auch auf der Portalfräse alle
Nichtmetalle.
Natürlich bietet PAF auch ein passendes Fahrwerk an, dessen Qualität sicher
tadellos ist. Allerdings ist es pneumatisch, und das Gefummel mit trennbaren
Schläuchen zum Flügel, Drucktank und Ventilen wollte ich mir ersparen. Somit
musste ich mir eine Alternative suchen, wofür ich erst die möglichen
Einbaumasse benötigte. Nach etwas hin und her war klar, dass die Electron
ER-30 Mechanik gut passen müsste. Da ich keine Musse hatte, alle Teile selbst
zusammenzustellen und am Ende doch das Falsche zu bestellen, habe ich die
Firma Electron (in Spanien zuhause) einfach gebeten, mir was passendes
zusammenzustellen. Nach einem äusserst freundlichen Mailwechsel mit den
Übermittlungen der Abmessungen fand dann, kurz vor dem Covid-19 Shutdown,
ein Paket mit einem Fahrwerkset feinster mechanischer Qualität, den Weg zu
mir.
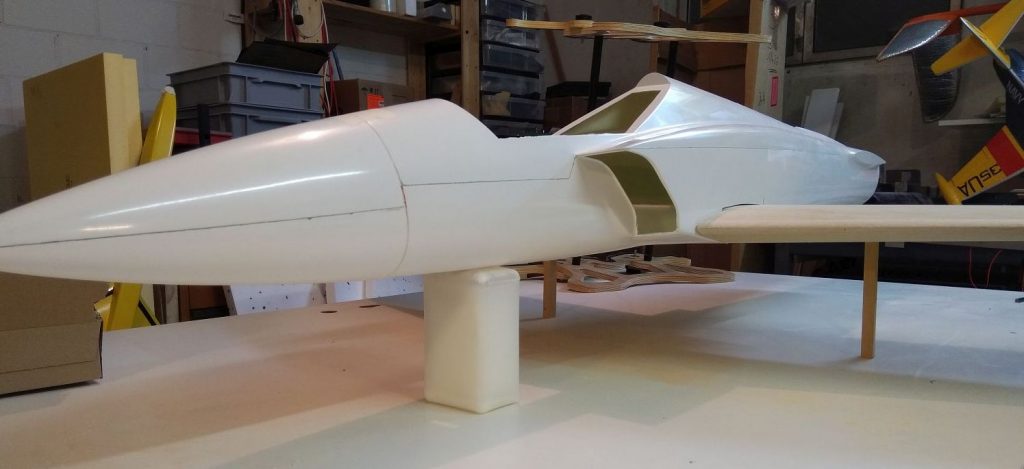
Bestimmung der Bugradbeinhöhe. Mit der Klarlackbuddel liegt die Rumpfachse
schön waagrecht…
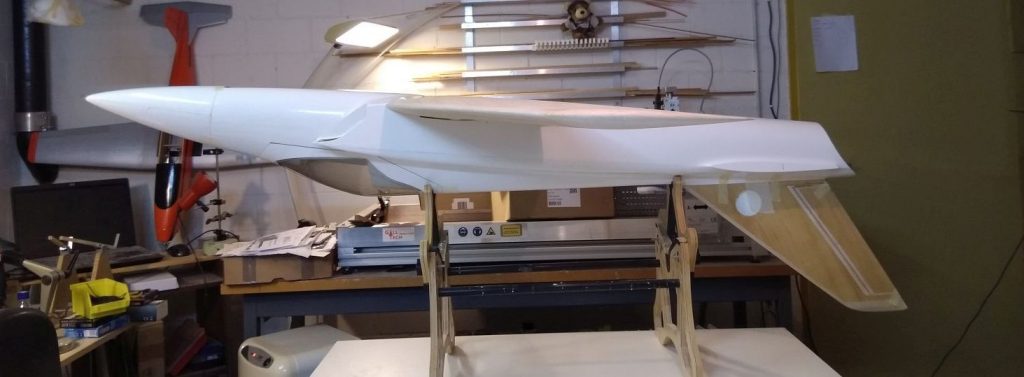
Hier noch ein zusammengesteckter Flieger zur weiteren (fotografischen)
Massbestimmung. Das musste auf dem Rücken geschehen, da sonst der Flügel
runterfällt…
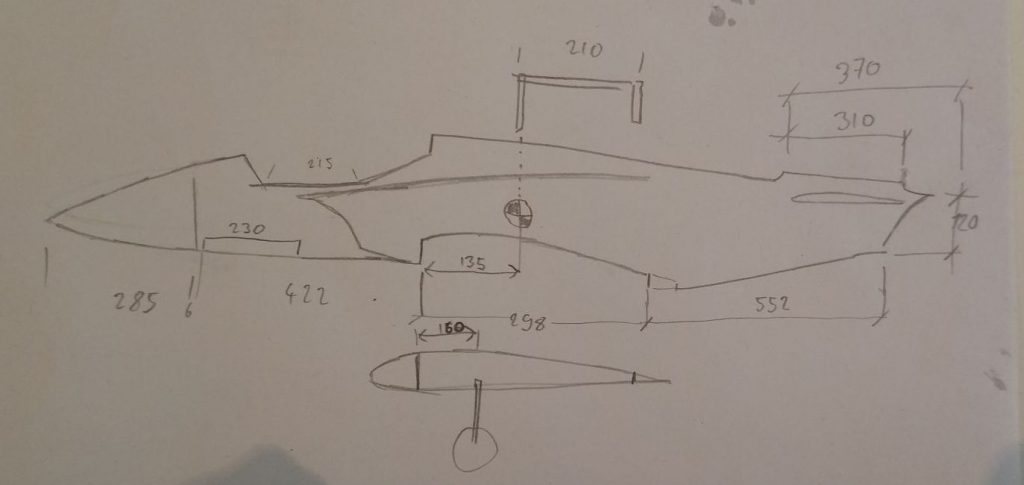
Das ist dabei herausgekommen…
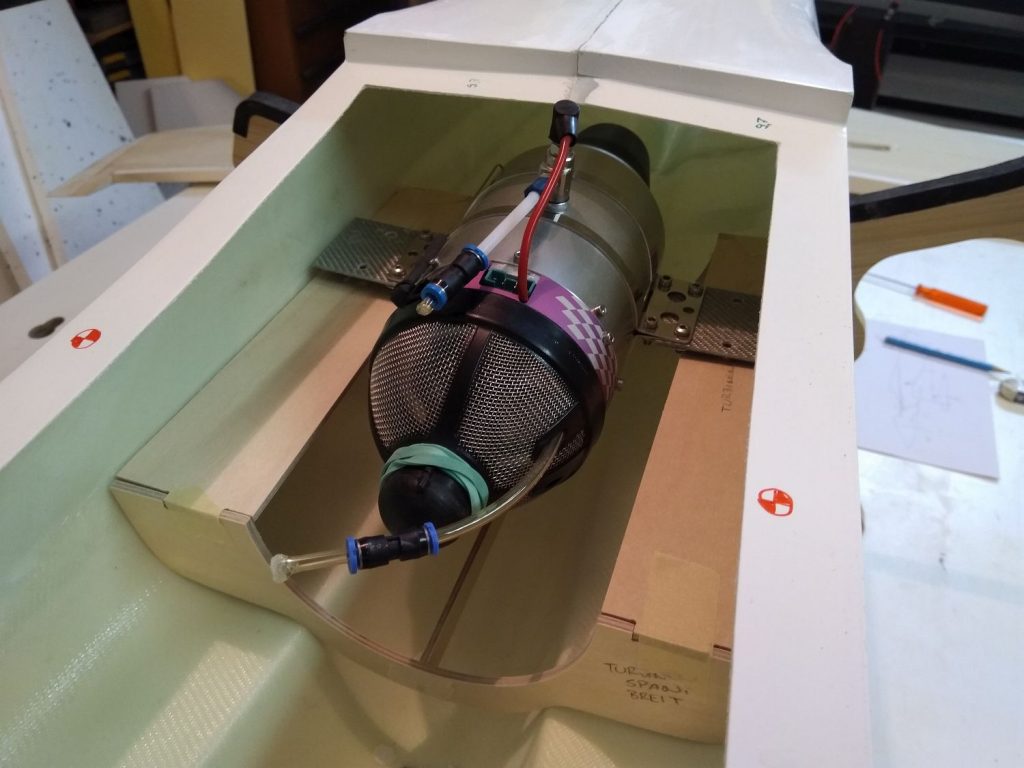
Gleich mal das Düsenbüsi mit ihrem neuen Plätzchen vertraut machen 😀
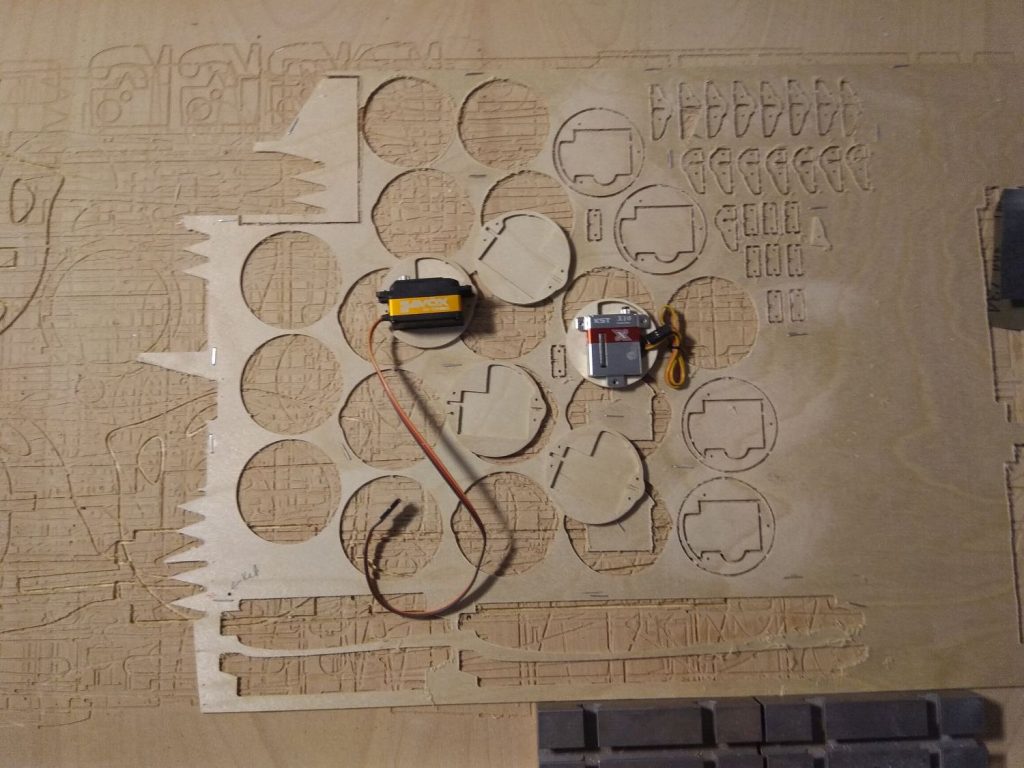
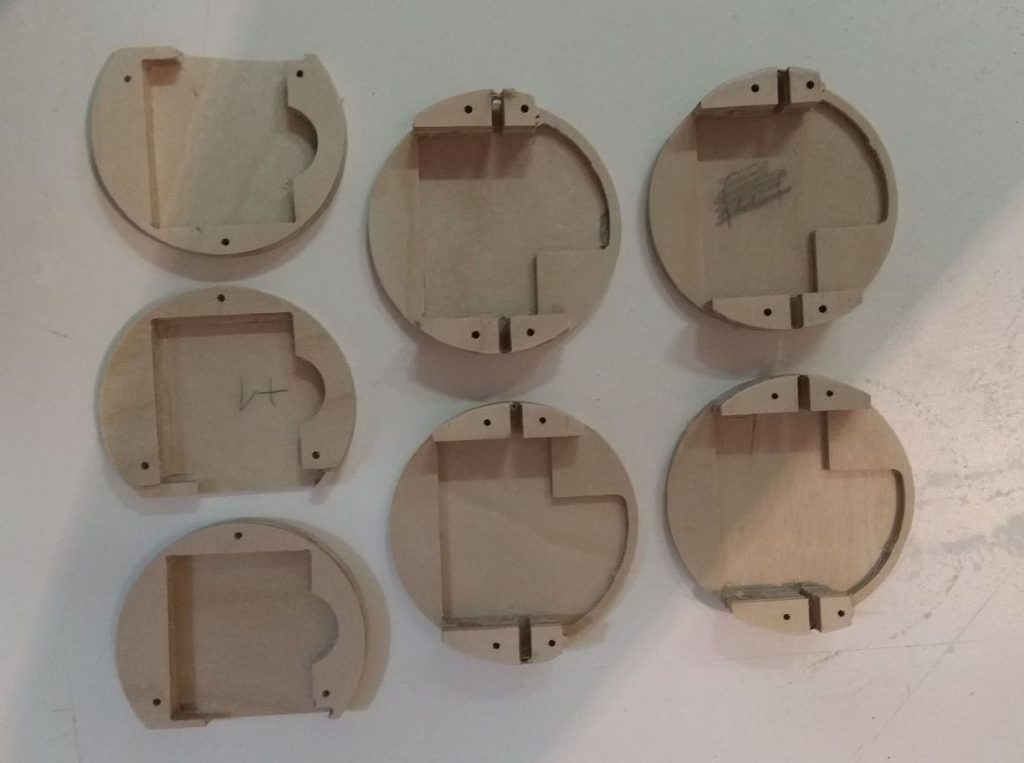
Die Wartezeit kann durch Servohalter fräsen verkürzt werden. Für die Ruder
habe ich jeweils ein KST X10 vorgesehen, für Querruder und Landeklappen
Savöx SV-1254MG. Beide Servos schienen mir ein guter Kompromiss aus Preis,
Gewicht und Leistung. Ausserdem sollten sie HV-tauglich sein.
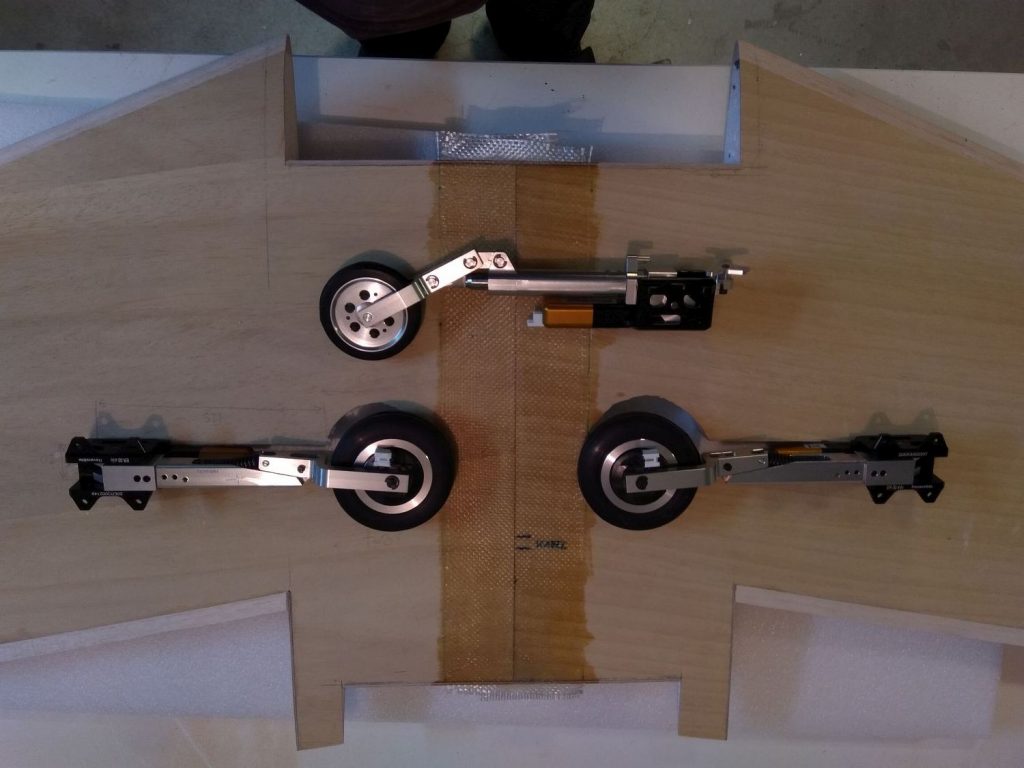
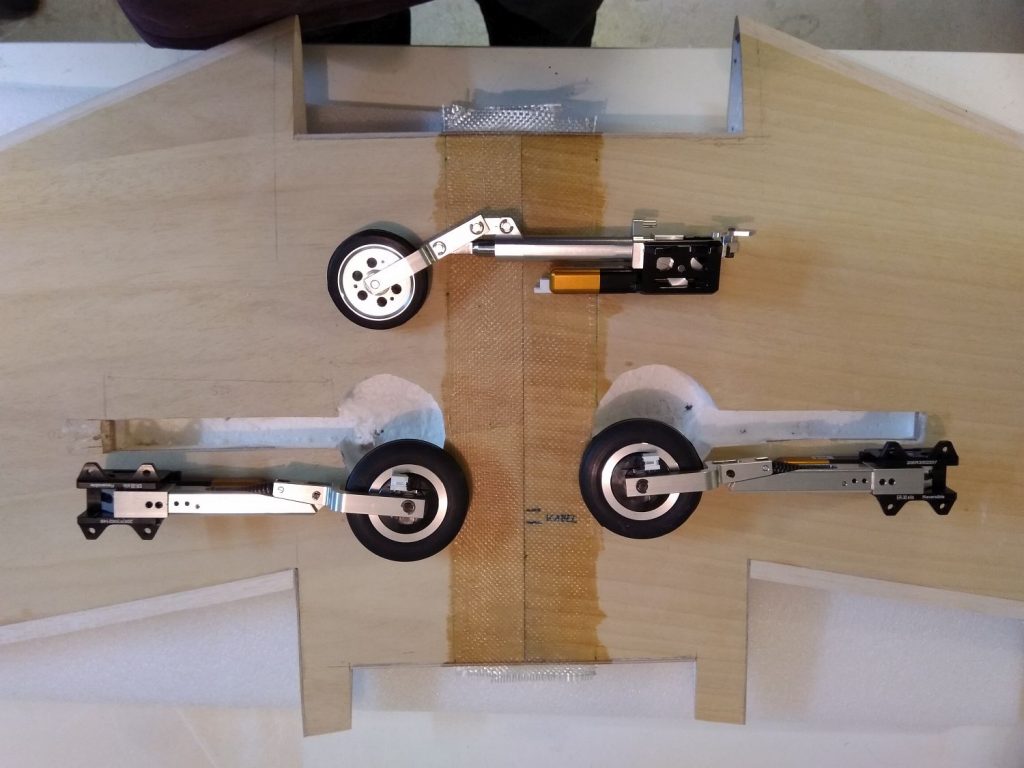
Mittlerweile sind die Flügel fertig verkastet und an der Verklebung mit 160g
Glasgewebe verstärkt. Was noch fehlt, ist der von PAF vorgesehene Sperrholz-
Holmteil im Schwerpunktbereich. Der kann aber erst eingebaut werden, wenn
die Fahrwerkausschnitte definitiv ausgefräst sind (die müssen noch dem
Elektron-Fahrwerk angepasst werden), denn sonst würde der Holm durch die
Ausschnitte gehen.
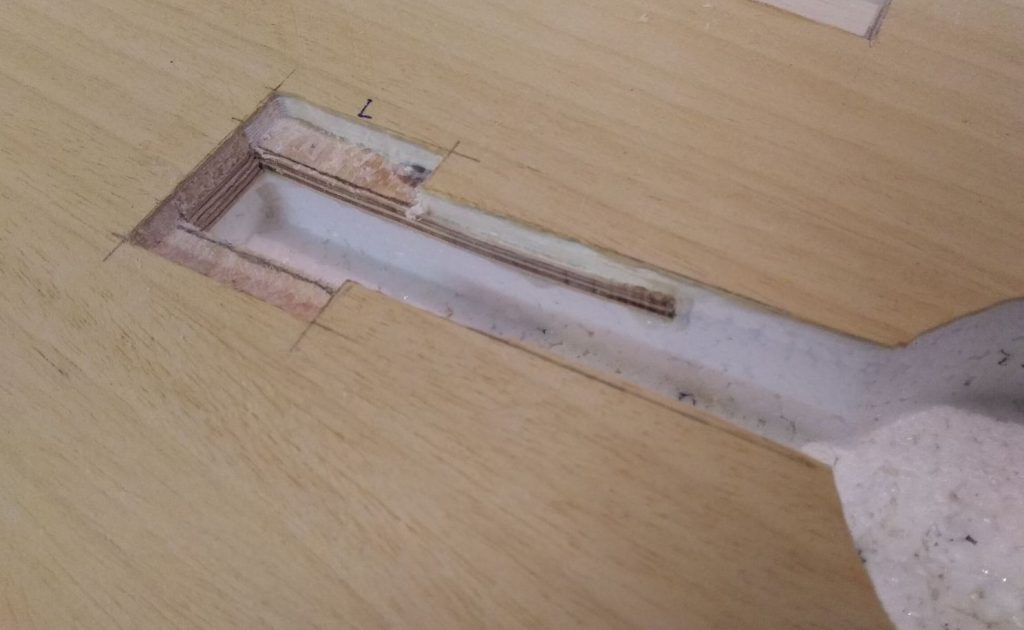
So sieht die freigefräste Fahrwerkhalterung aus. Für das Elektron-Fahrwerk
muss der Schlitz aber noch auf jeder Seite 1mm verbreitert werden, denn die
Mechanik ist etwas breiter. Sie ist auch tiefer, weswegen das Styro noch fast
komplett raus muss.
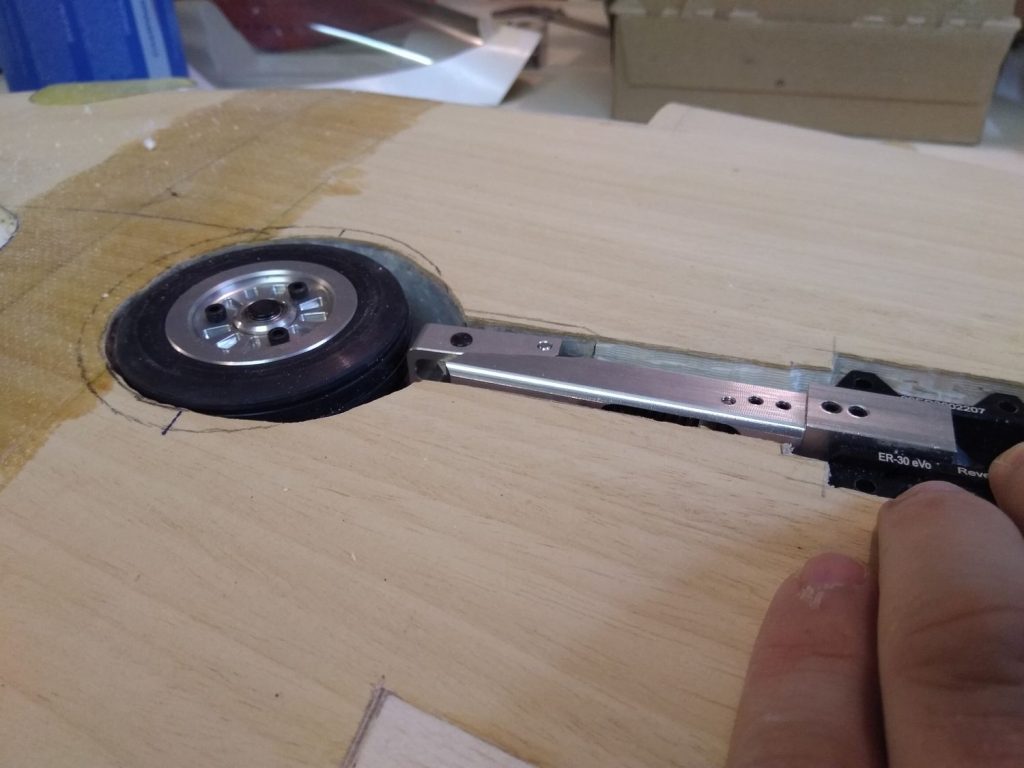
Passt, wackelt und hat Luft. Jetzt muss noch der Ausschnitt etwas vergrössert werden.
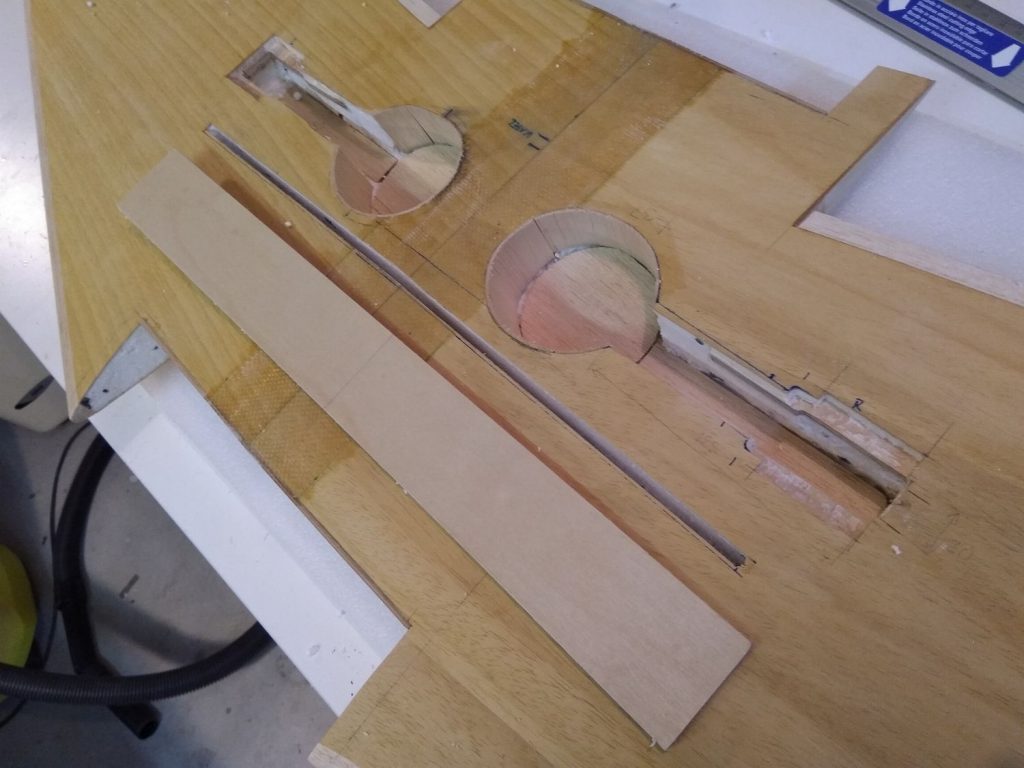
PAF sagt, dass der Sperrholzholm aus 6mm Sperrholz angefertigt sein muss. Als
ich die Platte aus 6mm Flugzeugsperrholz aus meinem Lager in der Hand hatte,
war mir klar, dass bei einem kapitalen Einschlag die Holmbrücke als einziges
Teil ganz überleben würde. Ich habe dann das 5mm Holz genommen und bin
auch da sicher, dass die Kraft, die das Teil aushält, nur teilweise in den Flügel
geleitet werden kann.
Den Ausschnitt in den Flügel habe ich von unten
vorgenommen, auf der oberen Beplankung gibts keinen Ausschnitt, da klebt das
Brett stumpf auf der Beplankung, was optimaler ist als unten. Der Sperrholzholm
ist 400mm breit. Die V-Form habe ich auf der Flügeloberseite abgenommen und
geschliffen, bis es passte. Die V-Form der Unterseite kann man mit dem Bleistift
anzeichnen, wenn man das Brettchen in den Schlitz steckt. Den Schlitz selbst
habe ich mit einer «Kataba Restauro Zugsäge» ausgesägt. Ein geniales Werkzeug,
um Holz und dünnes GFK (zB. Rumpfausschnitte) mit minimaler Schnittbreite
bolzengerade zu trennen. Der Name ist etwas irreführend, man kann auch an
Flugzeugen sägen, nicht nur an Zügen. Haha, Schenkelklopfer (es ist 02:20 Uhr,
sorry). Damit kommt man auch einigermassen sauber und senkrecht durch die
40mm Styropor bis zur Beplankung auf der anderen Seite. Mühsam ist dann
noch das herausklauben der hartnäckig an der Beplankung klebenden
Kügelchen. Die Klebefläche ist da unten dann auch nicht perfekt eben, weshalb
ich noch 2 Rovings zur Überbrückung und reichlich Mumpe (mit der Pipette,
damit sie nicht an den Styrowänden hängenbleibt) dazugegeben habe. Auch auf
der Oberseite habe ich zur Spaltfüllung mit Mumpe und einer Roving gearbeitet.
Auf dem Foto sieht man auch noch, wie ich die Radausschnitte mit leichtem
1,5mm Balsa schon mal etwas verkastet habe, das Styro habe ich nicht so sauber
herausgekriegt 🙁

So schaut das dann fertig und verschliffen aus.
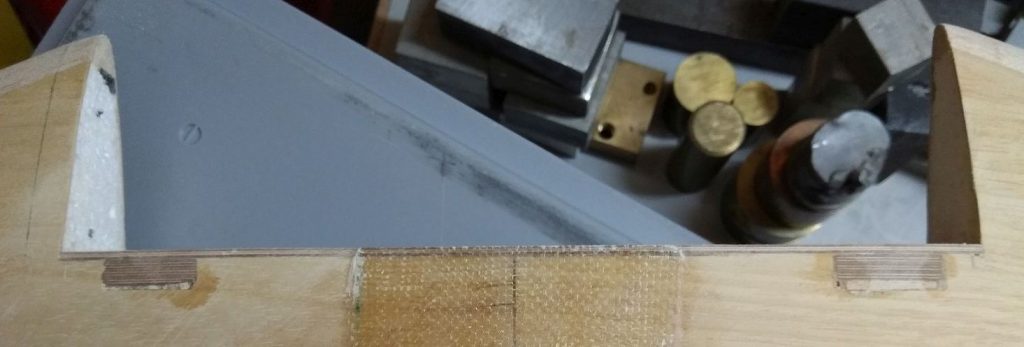
Kurz vor dem Beglasen der Fläche fiel mir noch ein, dass es keine schlechte Idee
wäre, die Verkastung noch ein bisschen zu verstärken, wo die in den Rumpf
greifenden Flügelbolzen hinkommen. Also noch an passender Stelle Beplankung
und Styropor abfräsen und etwas Fleisch in Form von Sperrholz einsetzen und
eben verschleifen und spachteln. Dann konnte die Fläche (Ruder und Leitwerke
schon 2 Wochen zuvor) endlich mit Nitro-Hartgrund gefillert, und dann mit 50g
Glasgewebe eingetucht werden. Jetzt härtet alles aus. Vorweg: Der klappenlose
Flügel ist jetzt 1115g schwer, davon gehen 126g zu Lasten der Glaserei.
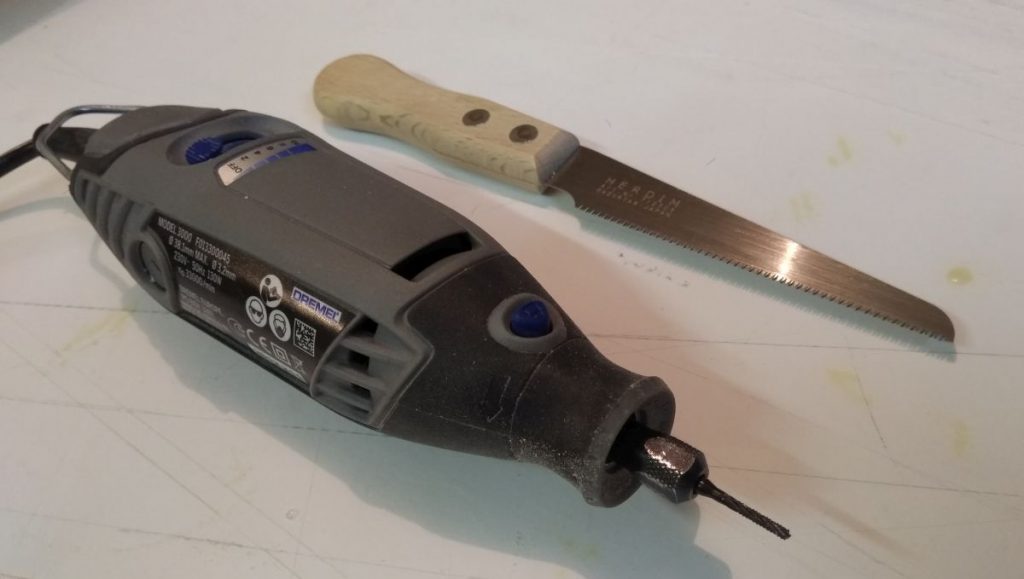
Zum Abschluss und Nachtrag noch ein Bildchen des erwähnten Fräsers und der
Säge.